Understanding Injection Molding Manufacture: A Comprehensive Overview
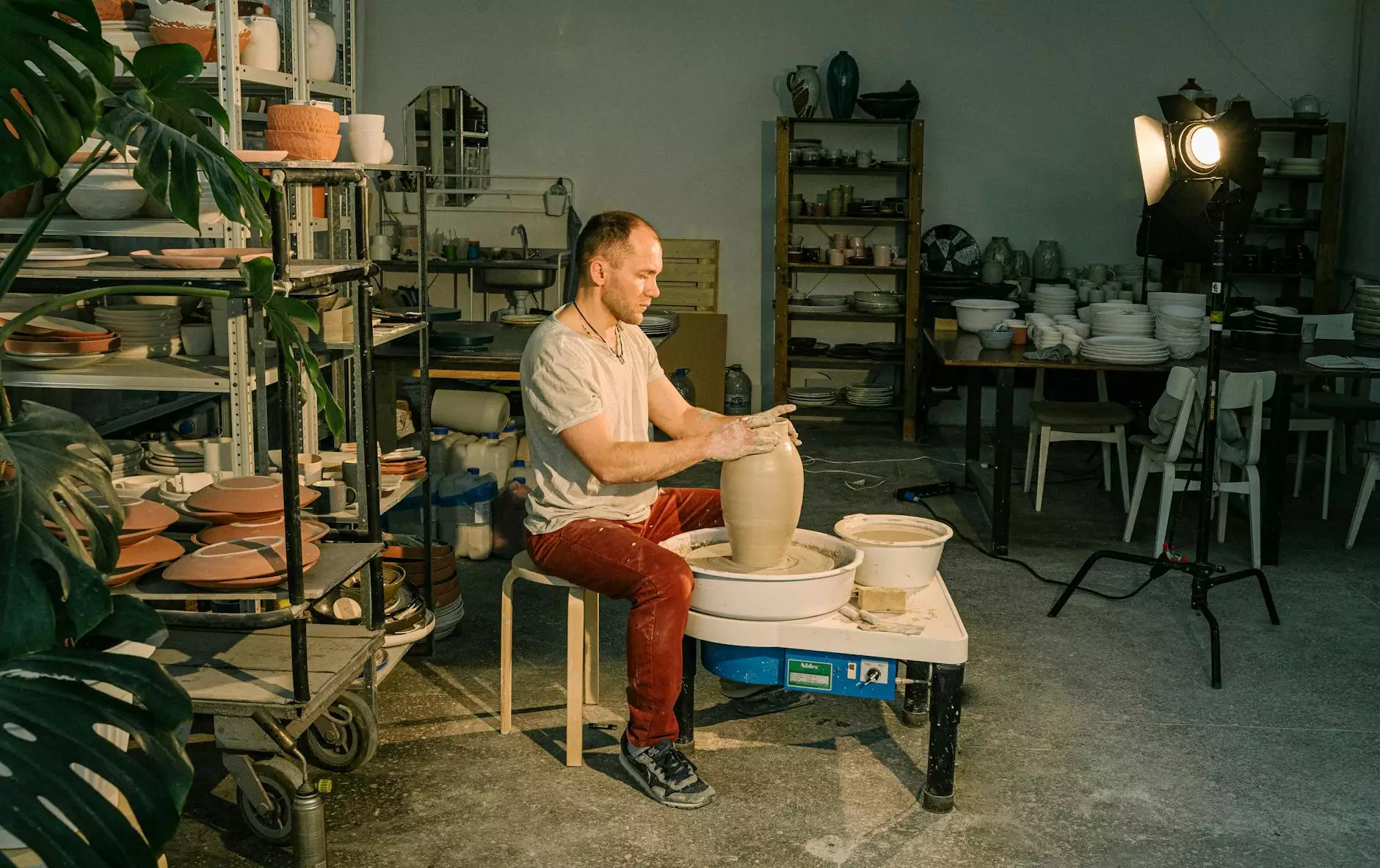
In the dynamic landscape of modern manufacturing, injection molding manufacture stands out as a pivotal process that enables the creation of durable and complex parts for various industries. This specialized technique, primarily employed in the production of plastic components, offers remarkable efficiency and precision. In this article, we will delve deep into the intricacies of injection molding, exploring its processes, benefits, applications, and the future landscapes of this manufacturing marvel.
What is Injection Molding?
At its core, injection molding is a manufacturing process used to create parts by injecting molten material into a mold. This method is widely adopted for making plastic products, but it can also be applied to metals, glass, and other materials. The beauty of injection molding lies in its ability to produce high volumes of identical parts with minimal waste, making it a cornerstone of production in various industries.
The Injection Molding Process
The injection molding process involves several key steps:
- Material Selection: Different materials can be used for injection molding, including thermoplastics, thermosetting plastics, and metals.
- Melting: The selected material is heated until it becomes a molten state, allowing it to flow easily into the mold.
- Injection: The molten material is injected into the mold at high pressure, filling the cavity and taking the shape of the mold.
- Cooling: Once injected, the material is allowed to cool and solidify, creating the desired part.
- Ejection: After cooling, the mold is opened, and the finished part is ejected.
Benefits of Injection Molding Manufacture
Injection molding manufacture offers numerous advantages that make it a preferred choice for businesses. Here are some of the key benefits:
- High Efficiency: Once the mold is created, the production process is rapid, allowing for high-volume production.
- Precision and Accuracy: Injection molding produces parts with tight tolerances, ensuring high-quality outputs.
- Minimal Waste: The process generates very little waste material compared to other manufacturing processes.
- Versatility: A wide range of materials can be used, allowing for the production of various products across different industries.
- Design Flexibility: Complex shapes and intricate designs can be achieved, making it ideal for innovative product development.
Applications of Injection Molding
Injection molding is utilized in numerous sectors, showcasing its versatility and capability. Here are some prominent applications:
1. Consumer Products
From household goods to toys, consumer products benefit greatly from injection molding. The durability and design options available allow manufacturers to create appealing and functional items that meet consumer demand.
2. Automotive Parts
The automotive industry relies heavily on injection molding for producing parts such as dashboards, door panels, and other components. The process ensures that parts can withstand rigorous use while maintaining aesthetic qualities.
3. Medical Devices
Injection molding is critical in manufacturing complex medical devices and components. Precision is key in this sector, and injection molding delivers high-quality parts essential for safety and functionality.
The Future of Injection Molding Manufacture
As technology continues to advance, the future of injection molding manufacture looks promising. Several trends are shaping the future of the industry:
1. Automation and Smart Manufacturing
With the rise of Industry 4.0, automation and smart technologies are entering the injection molding sector. This shift aims to enhance production efficiency, reduce human error, and optimize performance through data analytics.
2. Sustainable Practices
Environmental sustainability is becoming increasingly important. Injection molding manufacturers are exploring biodegradable materials and energy-efficient processes to reduce their carbon footprint.
3. Advanced Materials
Research and development into advanced materials are pushing the boundaries of injection molding, enabling the production of stronger, lighter, and more durable products.
Injection Molding in the Metal Fabrication Industry
While traditional perceptions of injection molding leans towards plastic parts, the technique is also making headway in metal fabrication. This hybrid approach allows for the production of metal parts with the same efficiency and precision that injection molding provides for plastics.
The Hybrid Process Explained
Hybrid injection molding combines the principles of traditional molding with metal injection molding (MIM). MIM allows for the production of small, complex parts made from metals and ceramics, which are difficult to fabricate using traditional machining methods.
Advantages of Metal Injection Molding
- Complex Geometries: This process enables the creation of intricate designs that would otherwise be challenging to achieve.
- Cost-Effectiveness: Producing high volumes of parts lowers costs significantly compared to traditional methods.
- Enhanced Properties: Metal injection molding results in parts with superior physical properties and surface finishes.
Choosing the Right Injection Molding Manufacturer
If you’re looking to partner with an injection molding manufacturer, it’s crucial to consider various factors:
- Experience and Expertise: Choose a company with a solid track record in injection molding and a portfolio that reflects your needs.
- Technology and Equipment: Ensure the manufacturer uses state-of-the-art technology to guarantee quality and efficiency.
- Quality Assurance: Look for manufacturers that offer robust quality control processes to maintain high standards.
- Material Options: A diverse range of material options is essential to ensure the right fit for your specific application.
Conclusion
In conclusion, injection molding manufacture is an indispensable aspect of modern manufacturing, offering a plethora of benefits and applications across various industries. Its efficiency, precision, and versatility make it an ideal choice for businesses looking to innovate and produce high-quality products. As we embrace the future of manufacturing, injection molding will undoubtedly play a significant role in shaping the industry standards and driving growth. With advancements in technology and a focus on sustainability, the potential for injection molding is boundless.
If you’re in the Metal Fabricators sector or any related fields, embracing injection molding could be your gateway to enhanced production capabilities and product innovation. For further inquiries and expert guidance, feel free to reach out to reputable manufacturers like Deep Mould, where quality meets precision in the world of injection molding.