Understanding and Solving Information Silos Problems in the Farming Equipment Sector
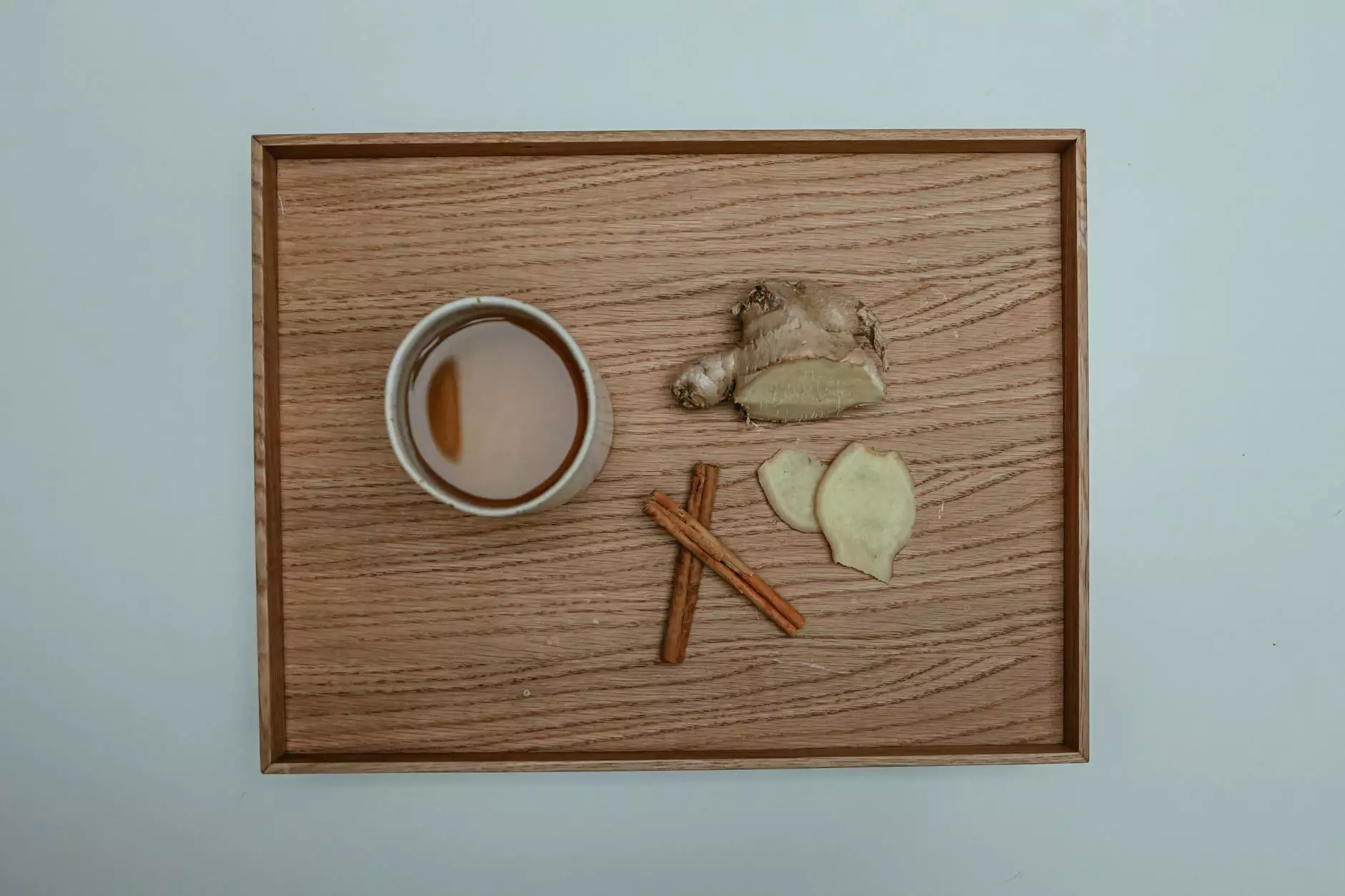
The concept of information silos refers to situations where information is stored within isolated systems, limiting accessibility and collaboration. This issue is particularly prevalent in the farming equipment repair industry, where communication breakdowns can lead to inefficient operations and lost opportunities. In this article, we delve deep into the information silos problems and explore practical strategies for overcoming these challenges, enhancing connectivity, and improving overall business performance.
What Are Information Silos?
Information silos are barriers that exist within an organization, preventing necessary data from flowing freely between departments or systems. In many cases, these silos are created by various departments utilizing different software solutions, leading to a lack of integration. As a result, important insights are often locked away instead of being readily available to teams that could benefit from them.
Consequences of Information Silos in Farming Equipment Repair
In the context of farming equipment repair, information silos can lead to several critical issues:
- Reduced Efficiency: When teams cannot easily access the information they need, repairs take longer, increasing downtime for equipment.
- Inconsistent Data: Different teams might collect and analyze data in different ways, leading to inconsistency and confusion.
- Poor Decision Making: When decision-makers do not have access to a holistic view of operations, their decisions may be based on incomplete information.
- Stifled Collaboration: Information silos can hinder collaboration between departments, reducing innovation and problem-solving capabilities.
Identifying Information Silos Problems
Recognizing the presence of information silos is the first step toward addressing them. Here are some signs that your farming equipment repair business may be facing these challenges:
- Frequent Miscommunication: If teams regularly report confusion regarding project statuses or company policies, it's likely they lack access to consistent information.
- Data Duplication: An excessive number of spreadsheets or reports that provide the same information can indicate siloed data.
- Low Employee Morale: Employees may feel frustrated if they cannot collaborate effectively or see the bigger picture due to lack of access to information.
- Delayed Responses: Slow responses to customer inquiries regarding repairs and services can be a direct outcome of siloed information.
Strategies to Overcome Information Silos in Farming Equipment Repair
Addressing information silos problems requires a strategic approach to enhance communication and collaboration. Below are several effective strategies:
1. Promote a Culture of Transparency
Encouraging a culture where transparency is prioritized will foster open communication. Leadership should share relevant data and insights across departments, empowering employees to make informed decisions.
2. Implement Integrated Software Solutions
Investing in integrated software solutions that connect different departments can greatly reduce silos. Look for platforms specifically designed for farming equipment repair that allow seamless sharing of data across various functions, such as inventory management, repair scheduling, and customer service.
3. Standardize Processes and Data Management
Establishing standardized processes for data collection and management can minimize discrepancies and inconsistencies. This includes creating templates for reports, adopting common metrics, and ensuring all team members are trained on using these standards.
4. Foster Interdepartmental Collaboration
Encouraging collaboration between teams can help break down silos. Consider organizing regular cross-department meetings where members share updates, challenges, and insights related to their work. This can lead to shared problem-solving initiatives and stronger working relationships.
5. Utilize Knowledge Management Systems
A robust knowledge management system enables teams to capture, share, and access valuable information easily. Implementing a centralized database where employees can store and retrieve information on repair processes, equipment manuals, and customer interactions can be a game-changer in reducing silos.
Benefits of Addressing Information Silos
By actively addressing information silos, businesses in the farming equipment sector can reap significant benefits:
- Increased Efficiency: Streamlined access to information results in faster decision-making and repairs.
- Enhanced Customer Service: With complete visibility into customer histories and equipment statuses, your team can respond to inquiries more effectively.
- Improved Employee Satisfaction: Employees are more likely to feel engaged and valued when they have access to the information they need.
- Stronger Business Agility: Organizations can adapt more rapidly to market changes and customer needs when all teams are aligned and informed.
Best Practices for Continuous Improvement
Addressing information silos problems is not a one-time task but a continuous effort. Here are some best practices to ensure ongoing improvement:
Regular Training and Development
Provide ongoing training for employees on collaborative tools and technologies that help break down silos. Regular workshops and skill-building sessions can develop a workforce capable of thriving in a connected environment.
Solicit Feedback and Iterate
Continuously seek feedback from employees about the effectiveness of communication and collaboration tools. Implement regular reviews that incorporate this feedback to refine processes and address emerging challenges.
Analyze Data and Performance Metrics
Make it a practice to analyze performance metrics that pertain to communication and teamwork. By regularly assessing what works and what doesn't, your organization can make data-driven adjustments aimed at reducing silos.
Conclusion
Information silos problems pose significant challenges to the farming equipment repair industry. However, with proactive strategies such as promoting a culture of transparency, implementing integrated software solutions, and fostering collaboration, these challenges can be effectively addressed. As organizations adopt these strategies, the benefits will manifest in greater efficiency, improved customer service, and enhanced employee satisfaction. By continuously refining these practices, businesses can ensure that they remain agile and responsive in a competitive landscape, setting the stage for sustained success in the farming equipment sector.