Unlocking Business Success with Rapid Plastic Prototyping in Metal Fabrication
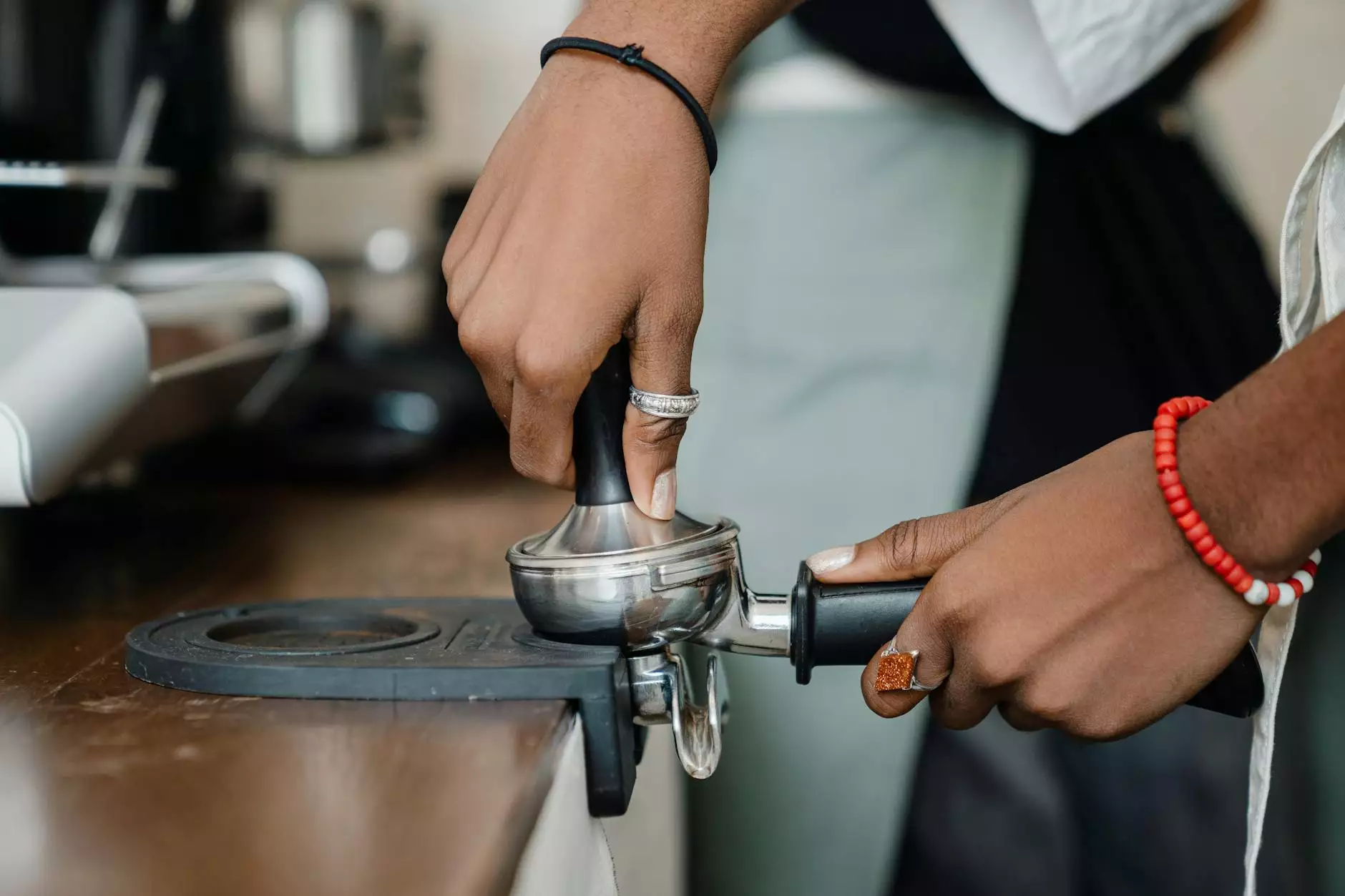
In today's highly competitive manufacturing landscape, innovation and speed are crucial to staying ahead of the curve. Rapid plastic prototyping has revolutionized the way businesses develop new products, particularly in the domain of metal fabrication. As a specialized metal fabricator, deepmould.net has harnessed the power of this cutting-edge technology to deliver superior solutions that accelerate product development cycles, minimize costs, and ultimately, enhance overall business success.
The Critical Role of Rapid Plastic Prototyping in Modern Business
Traditional product development methods often involve lengthy, costly processes with multiple iterations that can slow down time to market. Rapid plastic prototyping emerges as a game-changer by enabling rapid, precise, and cost-effective creation of prototype models that accurately represent final products. This ability to quickly test, evaluate, and refine designs directly influences the efficiency and profitability of manufacturing businesses, especially those involved in metal fabrication.
Understanding Rapid Plastic Prototyping
Rapid plastic prototyping is an additive manufacturing process that uses digital 3D modeling to produce plastic prototypes through techniques such as 3D printing, stereolithography (SLA), or selective laser sintering (SLS). While primarily associated with plastics, these techniques serve as invaluable tools for visualizing product concepts, testing ergonomic features, and validating design functionalities before progressing to metal parts manufacturing.
Why Rapid Plastic Prototyping Is Essential for Metal Fabricators
For metal fabricators, integrating rapid plastic prototyping into their workflows offers numerous strategic advantages:
- Accelerated Design Validation: Quickly produce prototypes that closely resemble final metal parts to verify fit, form, and function.
- Reduced Development Costs: Minimize expenses associated with traditional trial-and-error processes by identifying design flaws early.
- Enhanced Collaboration: Facilitate better communication among engineers, designers, and clients through tangible models.
- Improved Product Innovation: Experiment with complex geometries and innovative features without the high costs typically associated with metal manufacturing. Enhance your product development pipeline with rapid plastic prototyping to stay competitive and responsive to market demands.
Integrating Rapid Plastic Prototyping with Metal Fabrication Processes
The synergy between rapid plastic prototyping and metal fabrication is vital to modern manufacturing. This integration enables businesses to:
Design Iteration and Refinement
Prior to committing to expensive metal machining or casting, prototypes can be printed quickly to evaluate design features, ergonomics, and structural integrity. Feedback from these tests informs necessary modifications, reducing costly rework in the final metal parts.
Functional Testing and Evaluation
Plastic prototypes serve as stand-ins for metal components, allowing for rigorous testing of interaction, durability, and performance in real-world scenarios. This process ensures that only validated designs proceed to the final manufacturing phase, saving time and money.
Pre-Production Mockups
Using plastic prototypes as pre-production models enhances client presentations, marketing, and training materials, offering clients a tangible understanding of the final product—crucial for securing approvals and investments.
Technologies Behind Effective Rapid Plastic Prototyping
Several advanced technologies underpin successful rapid plastic prototyping, including:
- Stereolithography (SLA): Utilizes UV lasers to cure liquid resin into solid parts with high detail and surface finish—ideal for detailed prototypes.
- Fused Deposition Modeling (FDM): Extrudes thermoplastic filaments layer-by-layer, providing durable prototypes suitable for functional testing.
- Selective Laser Sintering (SLS): Uses laser energy to sinter powder materials, producing complex prototypes with better mechanical properties.
- PolyJet Printing: Jets photopolymer droplets onto a build platform, creating smooth, highly detailed prototypes that mimic production parts.
Choosing the appropriate technology depends on prototype requirements, including detail, strength, and turnaround time, which deepmould.net expertly manages to deliver optimal results.
Benefits of Choosing Deepmould.net for Your Rapid Plastic Prototyping Needs
Deepmould.net specializes in integrating advanced prototyping techniques within their metal fabrication services, ensuring clients benefit from:
- Unmatched Precision: State-of-the-art 3D printing equipment for high-resolution prototypes that mirror final designs.
- Speed and Efficiency: Fast turnaround times that accelerate project timelines.
- Cost-Effective Solutions: Competitive pricing without sacrificing quality, reducing overall project expenses.
- Expert Consultation: Skilled engineers guiding design optimization from concept to production.
- Comprehensive Service: End-to-end solutions covering prototype development, metal fabrication, and finishing techniques.
Case Studies: Transforming Business Outcomes with Rapid Plastic Prototyping
Case Study 1: Automotive Component Development
An automotive supplier collaborated with deepmould.net to create prototypes for a new engine component. Using SLA technology, they developed highly detailed plastic models that allowed for precise fitment tests and aerodynamic evaluations. This process shortened the development cycle by 40% and reduced costs associated with multiple metal prototype iterations.
Case Study 2: Medical Device Innovation
A medical device manufacturer utilized rapid plastic prototyping for ergonomic testing and functional validation of a new surgical tool. The rapid prototypes facilitated quick adjustments, leading to a final product that met strict regulatory and safety standards faster than traditional methods, ultimately improving time-to-market.
Choosing the Right Partner for Rapid Plastic Prototyping in Metal Fabrication
Partnering with a company like deepmould.net ensures that you receive:
- Expertise: Deep understanding of both plastic prototyping and advanced metal fabrication techniques.
- Custom Solutions: Tailored services that align with your specific project requirements.
- Technological Edge: Access to cutting-edge equipment and innovative processes.
- Proven Track Record: Successful projects across diverse industries including automotive, aerospace, medical, and consumer products.
- Customer-Centric Approach: Dedicated support to ensure your project exceeds expectations and delivers value.
Future Trends in Rapid Plastic Prototyping and Metal Fabrication
The ongoing evolution of rapid plastic prototyping is poised to bring even more transformative benefits to metal fabrication businesses:
- Multi-Material Printing: Combining plastics with functional materials for more realistic and versatile prototypes.
- Increased Automation: Streamlining processes for faster and more cost-effective production cycles.
- Enhanced Material Properties: Development of new polymers with properties that better simulate metals, enabling more comprehensive testing.
- Sustainable Solutions: Adoption of eco-friendly materials and processes that reduce environmental impact.
Final Thoughts: Embracing Innovation to Drive Business Growth
By fully leveraging rapid plastic prototyping, metal fabrication companies can significantly enhance their product development processes—reducing time-to-market, cutting costs, and improving product quality. Deepmould.net remains at the forefront of this technological revolution, providing clients with innovative, reliable, and efficient solutions that elevate their business potential.
Whether you're developing complex geometries, refining prototypes, or preparing for full-scale manufacturing, integrating rapid plastic prototyping into your workflow is a strategic move that will set you apart in a competitive marketplace. Embrace this technology today to unlock new levels of innovation and success.